Hintergrundinformationen zu optischen Spezifikationen
Fertigungsspezifikationen | Oberflächenspezifikationen | Materialspezifikationen
Optische Spezifikationen werden in der Konstruktion und Fertigung einer Komponente oder eines Systems verwendet, um zu beschreiben, wie gut bestimmte Anforderungen des Systems erfüllt werden. Wertvoll sind sie aus zwei Gründen: Erstens geben sie die akzeptablen Grenzwerte wichtiger Parameter an, von denen die Systemeigenschaften abhängen, zweitens geben sie an, wie viele Ressourcen (das heißt Zeit und Kosten) dafür bei der Fertigung aufgewendet werden dürfen.
Ein optisches System kann sowohl bei zu strengen als auch zu weit gefassten technischen Daten unzureichende Eigenschaften beisitzen, in beiden Fällen kann es zur Vergeudung von Ressourcen kommen. Nicht genau definierte technische Daten führen dazu, dass die erforderlichen Parameter nicht ordnungsgemäß bestimmt und daher die Eigenschaften unzureichend sind. Eine zu genaue Definition der technischen Daten liegt dann vor, wenn bei einem System Parameter zu genau definiert werden, ohne zu berücksichtigen, ob sich dadurch optische oder mechanische Eigenschaften ändern. Dies ergibt höhere Kosten und erschwert die Fertigung.
Um die Spezifikationen von optischen Komponenten genauer zu verstehen, müssen Sie zuerst deren Bedeutung kennen. Da die Zahl der Spezifikationen immer weiter wächst, betrachten wir hier nur die gebräuchlichsten technischen Daten zur Fertigung und für die Oberflächen- und Materialeigenschaften von Linsen, Spiegeln, und Fenstern. Filter, Polarisatoren, Prismen, Strahlteilern, Beugungsgittern, und Faseroptiken werden oft die gleichen Eigenschaften spezifiziert. Wenn man die wichtigsten Eigenschaften kennt und weiß, wie diese quantifiziert werden, hat man eine gute Ausgangsbasis für das Verständnis nahezu aller optischen Komponenten.
Durchmessertoleranz
Die Durchmessertoleranz einer runden Optikkomponente gibt den akzeptablen Wertebereich für den Durchmesser an. Diese Fertigungsspezifikation kann je nach den Fähigkeiten und Möglichkeiten des jeweiligen Herstellers schwanken, teilweise sogar je nach Fertigungsstandort desselben Hersteller. Obwohl die Durchmessertoleranz keinerlei Einfluss auf die optischen Eigenschaften der Optik selbst hat, ist sie ein sehr wichtiger mechanischer Toleranzwert, der berücksichtigt werden muss, wenn die Optik in einer Fassung montiert werden soll. Wenn der Durchmesser einer optischen Linse beispielsweise von seinem Nennwert abweicht, ist es möglich, dass die optische Achse und die mechanische Achse in einer Baugruppe nicht übereinstimmen und es damit zu einer Dezentrierung kommt (Abb.1). Typische Fertigungstoleranzen für Durchmesser sind +0,00/-0,10 mm bei Standardqualität, +0,00/-0,050 mm bei Präzisionsfertigungen und +0,000/-0,010 mm bei höchster Präzision.
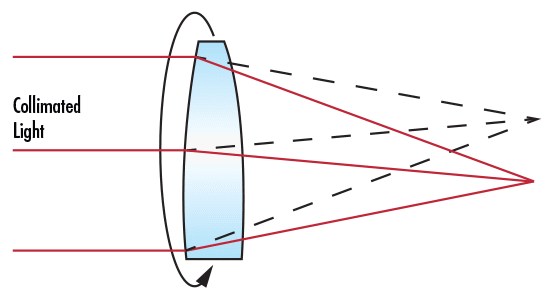
Figure 1: Dezentrierung von kollimiertem Licht
Mittendicke
Die Mittendicke einer Optikkomponente, meist einer Linse ist die in der Mitte gemessene Materialdicke einer Komponente. Die Mittendicke wird an der mechanischen Achse der Linse gemessen, das heißt an der Achse, die exakt zwischen den Außenkanten der Linse liegt. Schwankungen der Mittendicke einer Linse können die optischen Eigenschaften verschlechtern, weil die Mittendicke zusammen mit dem Krümmungsradius die optische Weglänge durch die Linse bestimmt. Typische Fertigungstoleranzen für die Mittendicke sind: ± 0,20 mm für Standardqualität, ± 0,050 mm für Präzisionsqualität und ± 0,010 mm bei höchster Präzision.
Krümmungsradius
Der Krümmungsradius wird definiert als der Abstand zwischen dem Scheitelpunkt einer Optikkomponente und dem Mittelpunkt der gedachten Kugel. Der Wert kann positiv, negativ oder unendlich sein, je nachdem, ob die Oberfläche konvex, konkav oder plan ist. Wenn der Wert für den Krümmungsradius bekannt ist, kann die optische Weglänge durch die Linse oder den Spiegel in Abhängigkeit von der radialen Position des Lichtsrahls ermittelt werden. Diese Ortsabhängigkeit der Weglänge hängt wiederum direkt mit der Brechkraft der Linse zusammen. Fertigungstoleranzen für den Krümmungsradius liegen in der Regel bei ± 0,5 %, bei Präzisionsanwendungen sind jedoch auch ± 0,1 % und bei extrem hochwertigen Anwendungen sogar +/- 0,01 % möglich.
Zentriergenauigkeit
Die Zentriergenauigkeit, auch als Zentrierung oder Dezentrierung bezeichnet, wird bei einer Linse als Strahlabweichung δ (Gleichung 1) angegeben. Wenn die Strahlabweichung bekannt ist, kann der Keilwinkel W mit einer einfachen Gleichung (Gleichung 2) berechnet werden. Die Dezentrierung einer Linse bezeichnet die physikalische Verschiebung zwischen der mechanischen Achse und der optischen Achse. Die mechanische Achse einer Linse ist die geometrische Achse der Linse und entspricht dem Zentrum des Außendurchmessers. Die optische Achse einer Linse wird durch die optisch wirksame, gekrümmte Oberfläche oder Oberflächen bestimmt. Zur Prüfung der Zentrierung wird eine Linse in einer Halterung platziert und angedrückt. Der Druck auf die Linse zentriert die erste gekrümmte Oberfläche automatisch in der Halterung. Die Halterung rotiert, wobei die Drehachse durch das Zentrum der Halterung und damit auch durch das Zentrum der ersten Linsenoberfläche läuft. Kollimiertes Licht, das entlang dieser Drehachse durch die Linse fällt, wird auf einen Punkt der Bildebene fokussiert. Wenn die Linse durch Drehung des Bechers rotiert, führt jede Dezentrierung der Linse dazu, dass der Brennpunkt wandert und einen Kreis mit dem Radius Δ auf der hinteren Brennebene beschreibt (Abb.1).
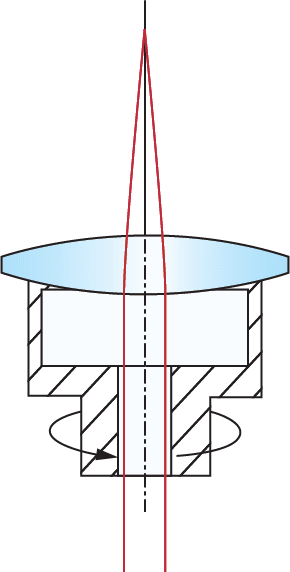
Abb. 2: Test zur Zentriergenauigkeit
Hierbei ist W der Keilwinkel, oft in Bogenminuten angegeben, und n der Brechungsindex.
Parallelität
Die Parallelität gibt an, wie parallel zwei Oberflächen zueinander liegen. Die Parallelität wird für Komponenten wie Fenster und Polarisationsfilter angegeben, bei denen parallele Oberflächen für die Systemeigenschaften ideal sind, weil sie Verzerrungen minimieren, die sonst die Bild- oder Strahlqualität verschlechtern. Typische Toleranzen liegen zwischen 5 Bogenminuten und einigen Bogensekunden.
Winkeltoleranz
Bei Komponenten wie Prismen und Strahlteilern entscheiden die Winkel zwischen den Oberflächen über die Eigenschaften der Optik. Diese Winkeltoleranz wird in der Regel mit einem Autokollimator gemessen. Der Autokollimator richtet die Optik mit Hilfe einer kollimierten Beleuchtung und deren Fresnelreflex auf der Oberfläche der Optik aus. Die Optik wird so lange gedreht, bis die Reflektion wieder in die Lichtquelle zurückgeworfen wird. Danach wird die nächste Oberfläche auf dieselbe Weise ausgerichtet. Die Winkeldifferenz zwischen den beiden ermittelten Positionen kann dann sehr präzise aufgezeichnet werden. Abbildung 3 zeigt das zugrundeliegende Prinzip eines solchen Autokollimators. Die Winkeltoleranz kann einige Bogenminuten bis einige Bodensekunden betragen.
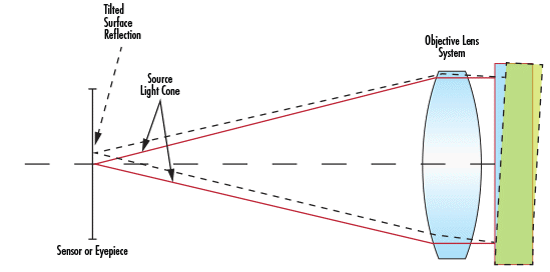
Abb. 3: Autokollimator-Konfiguration zur Messung der Winkeltoleranz
Fase
Glasecken können sehr zerbrechlich sein, daher ist es wichtig, sie beim Einbau und Transport einer Komponente zu schützen. Am häufigsten werden die Ecken dadurch geschützt, dass sie angefast werden. Schutzfasen schützen die Kanten und verhindern Ausbrechen. Schutzfasen werden durch ihre Stirnflächenbreite und den Winkel definiert (Abb.4).
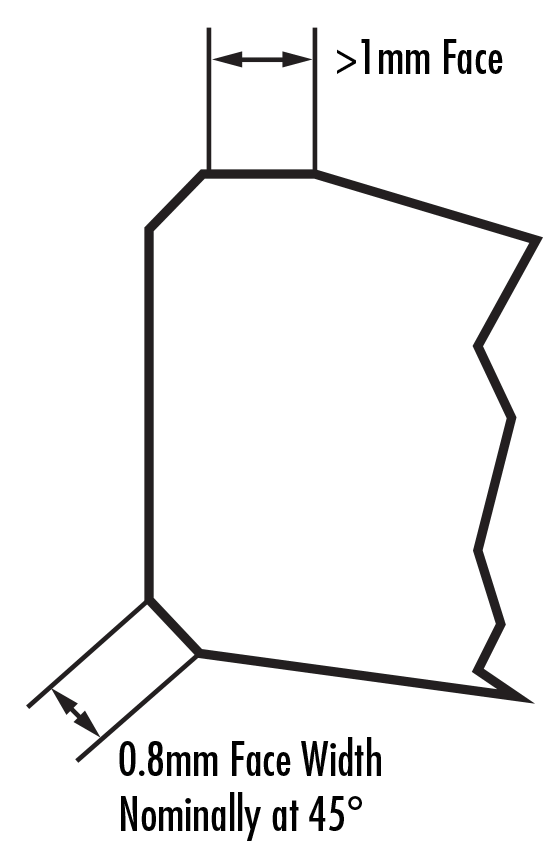
Abb. 4: Schutzfase einer optischen Linse
Schutzfasen haben in der Regel einen Schnittwinkel von 45°, die Fasenbreite richtet sich nach dem Durchmesser der Optik. Optiken mit einem Durchmesser unter 3,00 mm, beispielsweise Mikrolinsen oder Mikroprismen, werden in der Regel nicht angefast, da die Gefahr besteht, dass dabei die Kanten ausbrechen. Bei kleinen Radien oder starken Krümmungen, beispielsweise bei Linsen mit einem Durchmesser ≥0,85 x Krümmungsradius, wird aufgrund des großen Winkels zwischen der Oberfläche und der Kante der Linse teilweise keine Schutzfase benötigt. Für alle anderen Durchmesser sind die maximalen Fasenbreiten in Tabelle 1 angegeben.
Tablle 1: Fasentoleranzen | |
---|---|
Diameter | Maximale Fasenbreite der Schutzfase |
3,00 mm – 5,00 mm | 0,1 mm |
5,01 mm – 25,4 mm | 0,25 mm |
25,41 mm – 50,00 mm | 0,3 mm |
50,01 mm – 75,00 mm | 0,4 mm |
Freie Apertur
Die freie Apertur ist der Bereich einer Optik, in dem bestimmte Spezifikationen eingehalten werden müssen. Das betrifft zum Beispiel die Spezifikation der Oberflächenqualität. Außerhalb der freien Apertur kann der Hersteller nicht für die Einhaltung der angegebenen Spezifikationen garantieren. Das liegt in erster Linie an technischen Einschränkungen in der Fertigung. Es ist grundsätzlich nicht möglich, die Qualität über die volle Fläche der Optik zu garantieren. Typische freie Aperturen für Linsen finden Sie in Tabelle 2.
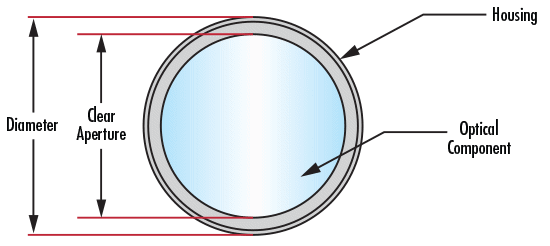
Abb. 5: Darstellung von freier Apertur und Durchmesser eines Filters
Tabelle 2: Toleranzen der freien Apertur | |
---|---|
Diameter | Freie Apertur |
3,00 mm – 10,00 mm | 90% of Diameter |
10.01mm - 50,00 mm | Diameter – 1 mm |
≥ 50,01 mm | Diameter – 1,5 mm |
Oberflächenspezifikationen
Oberflächenqualität
Die Oberflächenqualität einer optischen Fläche beschreibt ihr optisches Aussehen und berücksichtigt solche Mängel wie Kratzer, Ausplatzer und Löcher oder Einschlüsse. In den meisten Fällen sind solche Oberflächendefekte rein kosmetischer Art und beeinträchtigen die Systemleistung nicht wesentlich, sie können jedoch den optischen Durchsatz des Systems geringfügig reduzieren und das Licht etwas streuen. Bestimmte Oberflächen jedoch sind für solche Effekte empfindlicher: (1) Oberflächen in der Bildebene, weil auf die Defekte fokussiert wird und (2) Oberflächen, die hohen Lichtleistungen ausgesetzt sind, weil diese Mängel zu einer erhöhten Energieabsorption führen, was die Optik zerstören kann. Am häufigsten wird zur Bewertung der Oberflächenqualität die Scratch-Dig-Spezifikation der Norm MIL-PRF-13830B verwendet. Die Kratzer werden spezifiziert durch einen Vergleich der tatsächlich vorhandenen Kratzer mit einer kontrolliert verkratzten Referenzoberfläche, unter kontrollierten Lichtbedingungen. Die Scratch-Angabe beschreibt daher nicht den eigentlichen Kratzer, sondern ordnet ihm nur die ähnlichste Kategorie des MIL-Standards zu. Die Dig-Spezifikation bezieht sich dagegen direkt auf die Größe der Ausplatzer und Oberflächeneinschlüsse. Man nimmt den Durchmesser des größten Ausplatzers in Mikrometer, geteilt durch zehn, um die Dig-Angabe zu bekommen. Komponenten mit einer Scratch-Dig-Spezifikation von 80-50 gelten als Standardqualität, Spezifikationen von 60-40 als Präzisionsqualität und Spezifikationen von 20-10 als hochpräzise.Erfahren Sie hier mehr über Oberflächenqualität.
Oberflächengenauigkeit ebener Flächen - Planität
Die Oberflächengenauigkeit gibt die Abweichungen einer realen ebenen Fläche von der perfekten geometrischen Ebene an, sowie die eines Spiegels, Fenster, Prisma, oder Plano-Linse. Diese Abweichung kann mit einer optischen Planplatte gemessen werden. Eine optische Planplatte ist eine hochpräzise gearbeitete Planplatte, die als Referenzebene für die zu untersuchende Planoptik verwendet wird. Wenn die Referenzfläche und die zu prüfende Fläche aufeinander liegen, entsteht ein Interferenzmuster, dessen genaue Form Rückschlüsse auf die Abweichungen der beiden Ebenen zulässt. Wenn die Interferenzstreifen geradlinig, gleichmäßig verteilt sowie parallel sind, ist die geprüfte optische Oberfläche mindestens so eben, wie die verwendete Planplatte. Wenn die Interferenzstreifen gekrümmt sind, ergibt sich die Abweichung der Platten aus der Krümmung. Zur Auswertung legt man eine gedachte Linie durch die Enden eines Interferenzstreifens und eine zweite Linie, parallel zur Ersten, tangential and denselben Streifen. Die Zahl der Interferenzstreifen, die zwischen diesen Linien liegen, sind proportional zur Abweichung der beiden Platten, gemessen in Vielfachen der Wellenlänge λ des verwendeten Lichts. Ein Interferenzstreifen entspricht einer Abweichung von einer halben Wellenlänge. 1λ Oberflächenebenheit gilt als typische Güte, λ/4 Oberflächenebenheit als Präzisionsgüte und λ/20 als hochpräzise Güte.
Passfehler: Oberflächengenauigkeit gekrümmter Oberflächen
Die Genauigkeit der Radien gekrümmter Oberflächen ("Power") wird sehr ähnlich spezifiziert, wie die von planen Flächen. Geprüft wird ebenfalls die Abweichung zu einer hochpräzisen Referenzfläche, diese hat hier aber natürlich den passenden, exakt kalibrierten Krümmungsradius. Nach dem gleichen Prinzip wie zuvor, entstehen durch Luftspalte zwischen den beiden Flächen Interferenzmuster, die ein Maß sind für die Abweichung der Prüffläche von der Referenzfläche (Abb. 6). Eine Abweichung von der Referenzkomponente erzeugt eine Reihe von Ringen, die sogenannten Newtonschen Ringe. Je mehr Ringe vorhanden sind, umso größer ist die Abweichung. Die Anzahl der hellen bzw. der dunklen Ringe, nicht ihre Summe, entspricht dem doppelten Wellenlängenfehler.

Abbildung 6: Der Passfehler der Oberflächengenauigkeit gekrümmter Oberflächen wird durch Vergleich zu einer Referenzoberfläche oder unter Verwendung eines Interferometers gemessen.
'Der Passfehler der Oberflächengenauigkeit gekrümmter Oberflächen hängt eng mit dem Krümmungsradius zusammen. Dies wird durch folgende Gleichung beschrieben, bei der ∆R der Radienfehler, D der Linsendurchmesser, R der Oberflächenradius und λ die Wellenlänge (typischerweise 632.8 nm) ist:
(3)
Passfehler der Oberflächengenauigkeit gekrümmter Oberflächen in Wellen =
|
∆RD2
8R2 λ
|
Passfehler: Unregelmäßigkeit gekrümmter Oberflächen
Die Unregelmäßigkeit ("Irregularity") ist eine Spezifikation für die Oberflächengenauigkeit, die angibt, inwieweit die Form einer gekrümmten Oberfläche von der Form der Referenzfläche abweicht, unabhängig von der Abweichung des Krümmungsradius. Es werden also wortwörtlich die Unregelmäßigkeiten der Oberfläche erfasst, man könnte auch sagen die "Welligkeit" der Oberfläche. Diese Größe wird genauso bestimmt wie die Abweichung des Radius (Brechkraft), allerdings wird hier nicht die Zahl der Ringe betrachtet, sondern die Form. Die Ringe sollten kreisrund sein, Aweichungen davon deuten auf Unregelmäßigkeiten der Oberfläche hin. Wenn durch die Abweichung des Radius mehr als 5 Interferenzringe erzeugt werden, ist es schwierig, Unregelmäßigkeiten zu erkennen, die kleiner sind als 1 Interferenzring. Daher ist es allgemein üblich, bei Oberflächen ein Verhältnis zwischen den beiden Abweichungen von etwa 5:1 anzugeben. In der ISO-Norm, werden die beiden Größen unter "Passfehler" zusammengefasst, währen in der MIL-Norm tatsächlich "Power" und "Irregularity" angegeben werden. Detailliertere Informationen über optische Planplatten und die Auswertung von Interferenzmustern zur Prüfung der Ebenheit von Flächen und der Genauigkeit von gekrümmten Oberflächen finden Sie im Abschnitt Optische Planplatten.
Oberflächenrauhigkeit
Die Oberflächenrauhigkeit ist ein Maß für kleine Unregelmäßigkeiten auf einer Oberfläche. Sie sind in der Regel ein unerwünschtes Nebenprodukt des Poliervorgangs. Raue Oberflächen verschleißen schneller als glatte Oberflächen und sind für manche Anwendungen nicht geeignet, insbesondere für Anwendungen mit Laserlicht oder starker Wärme, da sich in den kleinen Rissen und Strukturen Hitzekeime bilden können. Die Fertigungstoleranzen liegen bei Standardprodukten im Bereich von 50 Å RMS (effektiv), bei Präszisionsprodukten bei 20 Å RMS (effektiv) und bei Produkten mit hoher Präzision bei 5 Å RMS (effektiv).
MATERIALSPEZIFIKATIONEN
Brechungsindex
Der Brechungsindex eines Mediums gibt das Verhältnis zwischen der Lichtgeschwindigkeit im Vakuum und der Lichtgeschwindigkeit in dem Medium an. Typische Brechungsindizes für Glas und sonstige optische Materialien liegen bei 1,4 bis 4,0; Gläser für das sichtbare Spektrum haben geringere Brechungsindizes als Materialien, die für Infrarotlicht gedacht sind. Ein verbreitetes Glas für das sichtbare Spektrum ist beispielsweise N-BK7. Es hat einen Brechungsindex von 1,517, während Germanium, ein für das Infrarotspektrum häufig eingesetztes Material, einen Brechungsindex von 4,003 besitzt. Weitere Informationen über Infrarotmaterialien finden Sie im Abschnitt Das richtige Material für Infrarot-Anwendungen. Der Brechungsindex eines optischen Glases ist eine wichtige Eigenschaft, weil die Brechkraft einer optischen Fläche sich sowohl aus dem Krümmungsradius der Fläche, als auch aus der Differenz der Brechungsindizes, der beiden angrenzenden Medien ergibt. Inhomogenitäten, die der Glashersteller angibt, beschreiben die Schwankungen des Brechungsindex im Glas. Inhomogenitäten werden in verschiedene Klassen eingeteilt, wobei Klasse und Inhomogenität im umgekehrten Verhältnis stehen. Je höher die Klasse, umso geringer die Inhomogenitäten (Tabelle 3).
Tabelle 3: Spezifikationen der Inhomogenität | |
---|---|
Inhomogenitätsklasse | Maximal zulässige Schwankung des Brechungsindex |
0 | +/- 50 x 10-6 |
1 | +/- 20 x 10-6 |
2 | +/- 5 x 10-6 |
3 | +/- 2 x 10-6 |
4 | +/- 1 x 10-6 |
5 | +/- 0.5 x 10-6 |
Abbe-Zahl
Eine andere Materialeigenschaft des Glases ist die Abbe-Zahl, die die Dispersion eines Glases angibt. Sie wird aus den Brechungsindizes eines Materials bei den Wellenlängen f (486,1 nm), d (587,6 nm) und c (656,3 nm) bestimmt. Der exakte Zusammenhang lautet

Typische Werte für die Abbe-Zahl liegen zwischen 25 und 65. Gläser mit einer Abbe-Zahl über 55 (weniger starke Dispersion) werden als Krongläser bezeichnet, Gläser mit einer Abbe-Zahl unter 50 (stärkere Dispersion) als Flintgläser. Dispersion bedeutet, dass sich der Brechungsindex eines Materials mit der Wellenlänge ändert. Am deutlichsten wird diese Eigenschaft dadurch, dass eine Linse für verschiedene Lichtwellenlängen eine etwas abweichende Brennweite besitzt. Detailliertere Informationen über wichtige Materialspezifikationen, wie Brechungsindex und Abbe-Zahl finden Sie im Abschnitt Optisches Glas.
Laserzerstörschwelle
Die Laserzerstörschwelle gibt die maximale Laserleistung pro Flächeneinheit an, denen eine Oberfläche ohne Schaden widerstehen kann. Dabei werden Werte für Impulslaser und Dauerstrichlaser (CW-Laser) angegeben. Die Laserzerstörschwelle ist eine sehr wichtige Materialspezifikation für Spiegel, da Spiegel in Lasersystemen häufiger eingesetzt werden, als jede andere Optik. Es sollte jedoch für jede lasergeeignete Optik eine Zerstörschwelle angegeben sein. Beispielsweise hat ein Ti: Saphir-Laserspiegel mit einer Laserzerstörschwelle von 0,5 J/cm2 bei 150 Femtosekunden Pulslänge und einer cw-Leistung von 100 kW/cm2. Das bedeutet, der Spiegel kann einer Energiedichte von 0,5 J/cm2 von einem im Femtosekundenbereich gepulsten Laser widerstehen oder 100 kW/cm2 eines Hochleistungslasers im Dauerbetrieb. Vor allem bei stark fokussierten Laserstrahlen sollten Sie darauf achten, dass die Zerstörschwelle nicht überschritten wird.
Es gibt zwar noch viele weitere Spezifikationen für die Fertigung, die Oberfläche und die Materialien, wenn Sie jedoch die geläufigsten optischen Spezifikationen kennen, können Sie Verwirrung leicht vermeiden. Linsen, Spiegel, Fenster, Filter, Prismen, Strahlteiler, Beugungsgitter und Faseroptiken haben eine Vielzahl von Eigenschaften; wenn Sie wissen, wie diese zusammenwirken und die Gesamteigenschaften eines Systems beeinflussen, können Sie leichter die besten Komponenten für die Integration in Optik-, Bildgebungs- oder Photonik-Anwendungen auswählen.
weitere regionale Telefonnummern
ANGEBOTSTOOL
Geben Sie zum Starten die Produktnummer ein.
Copyright 2023 | Edmund Optics, Ltd Unit 1, Opus Avenue, Nether Poppleton, York, YO26 6BL, UK
Die Edmund Optics GmbH Deutschland fungiert als Handelsvermittler für die Edmund Optics Ltd. in Großbritannien.
Vertragspartner ist die Edmund Optics Ltd. in Großbritannien.